あまりこだわったことがない、基板加工にも今回は、取り付け位置の制限などから外形加工をする必要があったのだが、使ったP板CADはKiCADにしたところ、基板加工機CIP100に付属してきたOriminでは対応できないことが分かり、急遽今まで使っていたPCBEで加工データの位置を取り込んで穴加工とその配線を通すという形になった。昔でいうところのアートワークを引いている感じだ。
作りたい基板サイズは45×105ほどなのでCIP100(Max 160×100)としては二枚取りが出来そうなあんばいなので外枠の一部は今回基板の縁に添わせる形で刃物の摩耗も防ぐことにした。取り付ける部品を押える目的のインシュロックを通す必要もあって角穴データは溝切の一環で外形データと通すことが出来たのだが、基板自体は四角にしかすることが出来ず一部を切り込んだ形にはできないことが判明した。対策は簡単に切り落とせそうな角穴をその位置近くに置くという代替案だ。KiCADで通らなかったデータにはDCジャックのランドパターンもあったようだが、これは少し大きめのパッドで逃げることにした。
本番の基板とパターンと部品配置だけを似せた状態でのデバッグということになる。試作動作完了となれば、基板発注という展開になる。
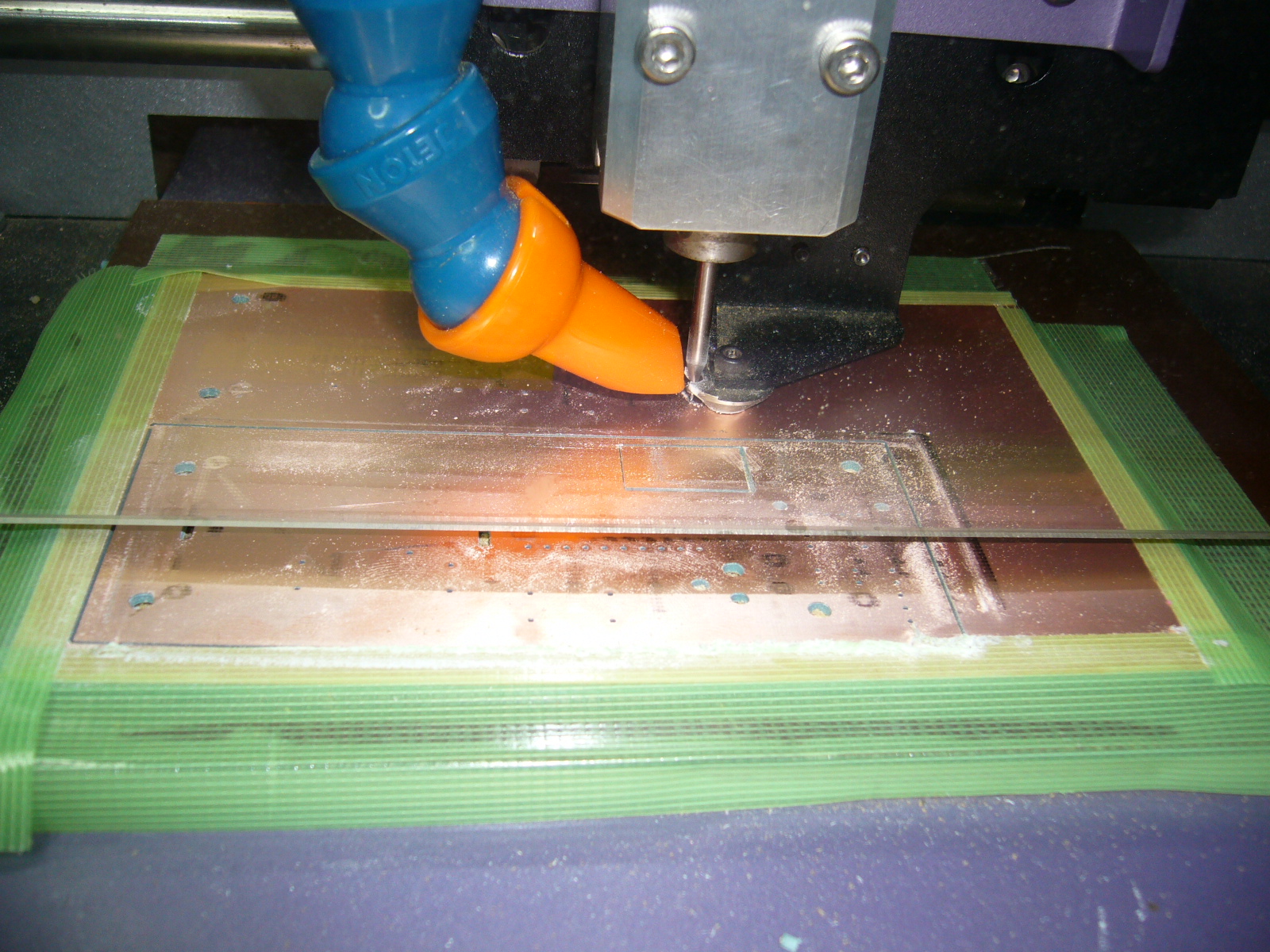